Sand Mold Casting Services
Sand Casting Excellence with LK tools
LK tools stands at the forefront of the global manufacturing stage as a premier provider of sand casting services. Renowned for our commitment to quality and efficiency, we offer a spectrum of high-quality metal casting solutions designed to meet the diverse needs of industries around the world.
Sand casting, a time-honored process with a rich history, continues to thrive as a preferred method for metal part fabrication thanks to its cost-effectiveness and versatility. This technique is particularly advantageous for producing large components and is celebrated for its ability to accommodate a vast array of metals and complex geometries.
Why Sand Casting with LK tools?
Cost-Effective: Sand casting is an economical choice for both low and high-volume production runs. The relatively low cost of mold materials and equipment, combined with the simplicity of the process, translates to significant savings for our clients.
Versatility: Our sand casting service is adept at handling a wide range of metals, including iron, steel, aluminum, bronze, and more, providing flexibility in material selection to suit the specific requirements of any project.
Efficiency: The sand casting process is streamlined to minimize lead times, ensuring that projects move from design to production
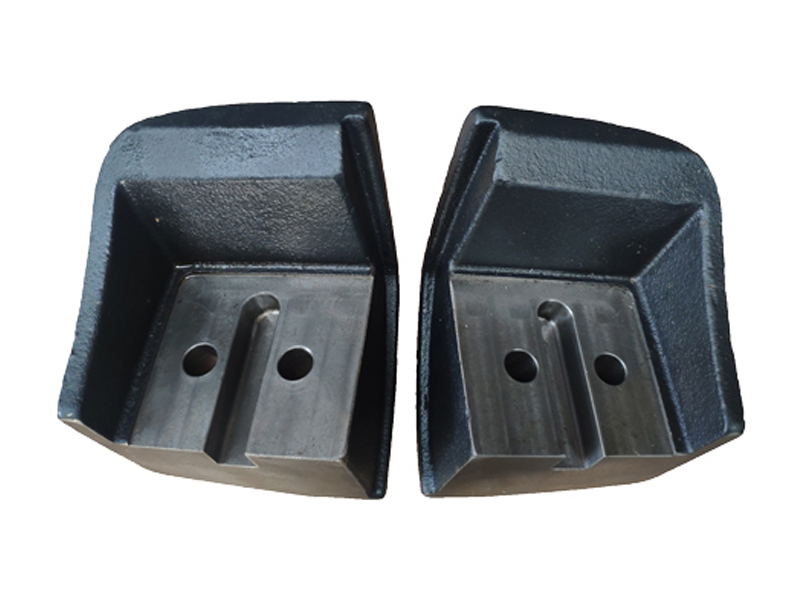

Understanding Sand Casting: A Fundamental Metal Manufacturing Technique
Sand casting is a traditional metal casting process that has stood the test of time due to its versatility and cost-effectiveness. At its core, sand casting involves the use of specially formulated sand to form molds into which molten metal is poured, solidifying to create a metal product. This method is revered for its ability to produce a vast array of metal parts, from small components to large machinery pieces.
The Process of Sand Casting
The sand casting process begins with the creation of a pattern that represents the shape of the desired part. This pattern is typically made from materials such as wood, metal, or plastic, and it serves as a template for the mold.
Once the pattern is ready, it's placed inside a flask and packed with sand, which has been mixed with a binding agent to help it retain its shape. The sand forms around the pattern, creating a cavity that is an exact negative of the part to be cast.
After the sand mold is compacted and solidified, the pattern is carefully removed, leaving the cavity into which the molten metal will be poured. Depending on the complexity of the part, the mold may consist of two or more sections that fit together precisely.
The next step is the pouring of the molten metal into the sand mold. The metal is heated to its melting point and then carefully poured into the mold's cavity. The high temperature of the molten metal causes the sand to harden further around it, capturing intricate details and ensuring the final product's accuracy.
Once the metal has cooled and solidified, the sand mold is broken apart to reveal the newly formed metal part. The part is then
swiftly. This efficiency is a key factor in reducing overall project costs and meeting tight deadlines.
Customization: With the ability to create molds for parts of various sizes and complexities, sand casting is an ideal option for custom metal part fabrication. We work closely with our clients to produce parts that are tailored to their unique specifications.
At LK tools, we harness the capabilities of sand casting to deliver components that exhibit the desired strength, durability, and dimensional accuracy. Our process begins with the creation of a sand mold, crafted to mirror the negative space of the intended part. Molten metal is then poured into this mold and left to solidify. Once cooled, the sand is broken away to reveal the cast metal part, which can then undergo finishing processes to achieve the final desired appearance and properties.
Our expertise, combined with a thorough understanding of the intricacies of sand casting, positions LK tools as a trusted partner in the manufacturing industry. Whether you're seeking large-scale production or custom prototypes, our sand casting services are engineered to provide reliable results that align with your project goals.
For more information about our sand casting capabilities or to discuss how we can assist with your next project, please contact LK tools. We are dedicated to delivering excellence in metal casting and ensuring that your experience with us is not only satisfactory but exceeds expectations.

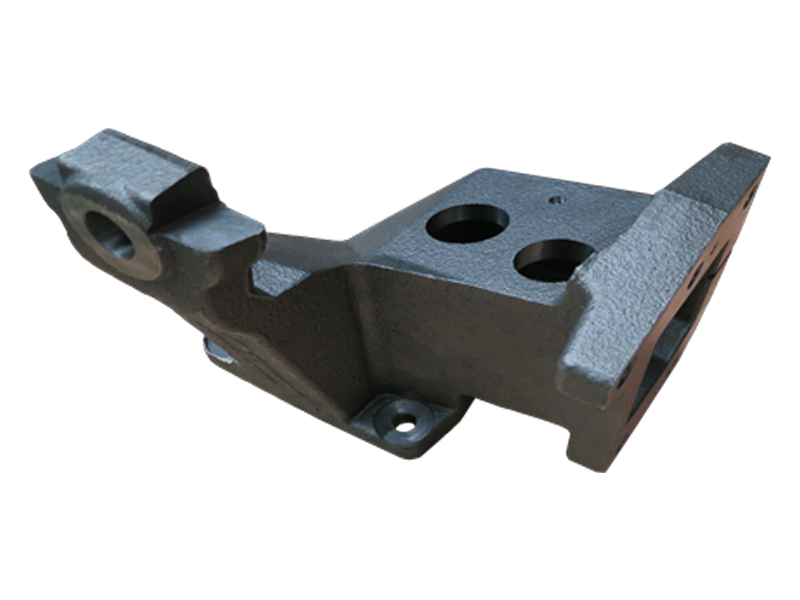
taken through various finishing processes, such as grinding, machining, or sandblasting, to remove any excess material and achieve the required surface finish.
Advantages of Sand Casting
Flexibility in Size and Shape: Sand casting can produce parts of virtually any size and complexity, from small gears to large engine blocks, with intricate internal cavities and details.
Material Diversity: A wide range of metals can be used in sand casting, including iron, steel, aluminum, bronze, and brass. This flexibility allows manufacturers to choose the most appropriate material for the part's intended use.
Cost-Efficiency: The materials used for creating sand molds are relatively inexpensive, and the equipment required for sand casting is less costly than other casting methods. This results in lower production costs, especially for small to medium-sized production runs.
Ease of Modification: Changes to the design of the part can be easily accommodated by modifying the pattern or adjusting the sand mold, making sand casting an excellent option for prototypes and custom parts.
Sand casting remains a popular choice for manufacturers due to these advantages and the quality of the parts it can produce. Whether for low-volume custom work or high-volume production, sand casting is a reliable and efficient method for creating metal parts in a wide range of industries.
The Intricacies of Sand Casting: From Pattern to Metal Part
Sand casting is an intricate process that transforms raw metal into precisely shaped parts through a series of detailed steps. Here is a closer look at how this time-tested method works to create a wide variety of metal parts.
Pattern Creation and Gate System
The journey of a sand-cast part begins with the creation of a pattern, which is a replica of the final part to be produced. This pattern is typically crafted from wood, metal, or plastic and serves as a blueprint for the mold. Along with the pattern, a gate system is designed. This system consists of a series of channels, including a pouring cup and a sprue, which facilitate the flow of molten metal into the mold cavity.
Molding with Cope and Drag
The next step involves preparing a two-part casting flask that consists of the cope (the top half) and the drag (the bottom half). The mold pattern is strategically placed within the sand, and the gate system is set up to connect with the mold cavity. Once the sand is packed firmly around the pattern and gate system, the pattern is carefully removed, leaving behind an impression that forms the mold cavity.
Melting and Pouring Metal


Mastering the Art of Sand Casting: A Breakdown of Essential Components
Sand casting is a multifaceted process that requires precision and an understanding of various components that come together to create metal parts. Each element of sand casting plays a critical role in ensuring the accuracy and quality of the final product. Here, we dissect the key components involved in sand casting and their functions:
Pattern: The Blueprint for the Part
The pattern is the cornerstone of the sand casting process. It's a physical model of the part to be cast and is usually made from materials like wood, plastic, or metal. The pattern is designed to be slightly oversized to account for the shrinkage of metal during cooling. It's used to shape the cavity within the sand mold where the molten metal will be poured.
Mold: The Sand Structure
The mold is what gives form to the cast part. It's created by packing a special sand mixture around the pattern. Once the sand hardens, the pattern is removed, leaving a cavity in the shape of the part. The mold consists of two main sections: the cope (the upper half) and the drag (the lower half), which come together to form the complete mold cavity.
Core: The Architect of Internal Geometries
Cores are utilized when the part design includes internal cavities or undercuts that cannot be shaped by the pattern alone. Made of sand or metal, cores are strategically placed in the mold cavity to form these complex internal features. They remain in the mold until the molten metal is poured and then are removed once the metal has solidified.
Pouring Cup and Sprue: The Pathway for Molten Metal
With the mold prepared, the metal is subjected to high temperatures until it reaches a molten state. Different alloys have varying melting points, and some metals may require more time to heat adequately. Once the metal is fully molten, it is poured into the mold cavity through the gate system.
Cooling and Mold Removal
As the metal cools within the mold, it begins to solidify into the shape of the final part. This cooling process is crucial as it determines the structural integrity and detail replication of the cast part. After the metal has solidified, the sand mold is broken apart along a predetermined parting line to reveal the newly formed metal part. While the sand mold is destroyed during this process, the pattern remains intact and can be reused for future molds.
Reusable Patterns and Non-reusable Molds
One of the unique aspects of sand casting is the contrast between the reusable nature of the mold pattern and the single-use sand mold. While the former can be employed repeatedly to create multiple parts, each sand mold can only be used to produce one part, as it is destroyed to extract the solidified metal. This is a trade-off that allows for the customization and flexibility of sand casting, enabling manufacturers to produce parts with complex shapes and intricate details.
Sand casting is a versatile and reliable process that has been utilized for centuries to create everything from small components to large industrial parts. Its ability to handle diverse materials and geometries makes it a staple in the manufacturing world. By understanding the process of sand casting, manufacturers can continue to harness its potential to create high-quality, cost-effective metal parts for a range of applications.
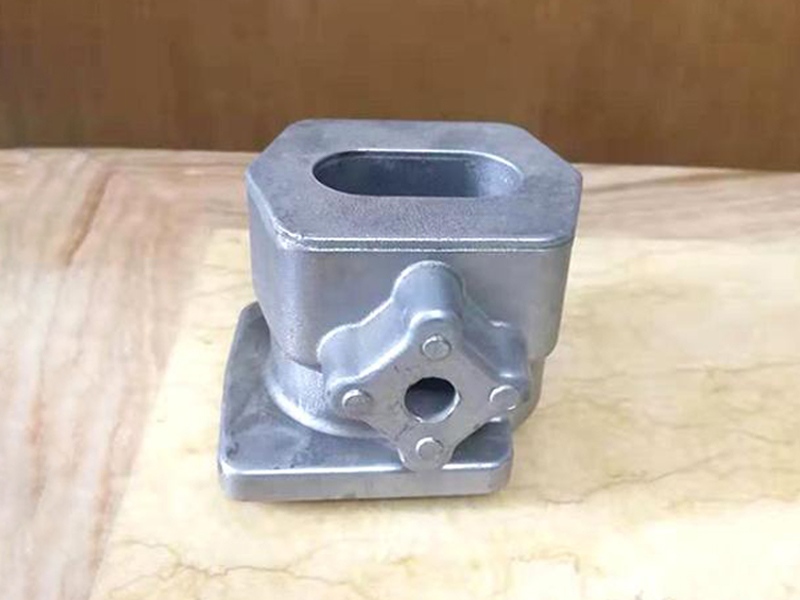
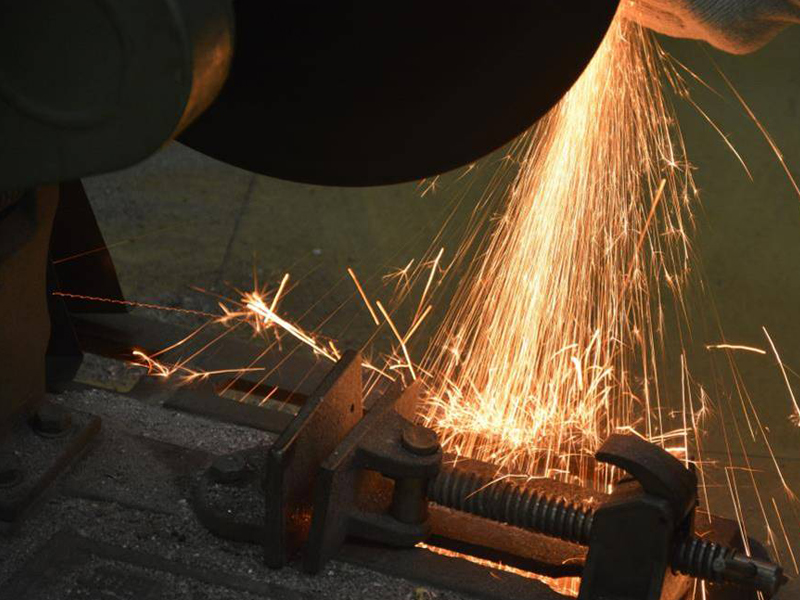
The pouring cup and sprue create the entry point and channel through which the molten metal is introduced into the mold. The pouring cup serves as the initial receptacle for the molten metal, and the sprue guides it from the pouring cup into the main gating system of the mold.
Risers: Guardians against Shrinkage
Risers, also known as feeders, are reservoirs of molten metal connected to the mold cavity. Their purpose is to feed additional metal into the cavity as the casting cools and shrinks, preventing cavities and other defects that can occur due to metal contraction.
Gating System: The Director of Metal Flow
The gating system is a network of channels designed to control and direct the flow of molten metal into the mold cavity. It includes runners and gates that regulate the speed and pressure of the metal, minimizing turbulence and ensuring a consistent fill of the cavity.
Molding Flask: The Supporting Framework
The molding flask is a box-like container that holds the sand mold in place during the casting process. It provides support and stability to the mold and is constructed in such a way that it can be easily separated to remove the finished mold.
Together, these components of sand casting interact seamlessly to create a precision mold into which molten metal can be poured and solidified to form the desired metal part. With careful design and execution, sand casting allows for the production of parts with complex geometries and internal passages, making it a versatile and invaluable process in the world of metal manufacturing.
Determining the Suitability of Sand Casting for Your Product
When deciding on the appropriate manufacturing process for your product, sand casting often emerges as a contender due to its cost-effectiveness and adaptability. However, it's essential to assess whether sand casting aligns with the specific needs of your project. Below are key factors to consider when evaluating if sand casting is the right choice for manufacturing your product.
Quantity: Scale of Production
Sand casting is particularly advantageous for small to medium production runs. For large quantities, alternative methods like die casting or investment casting may offer greater efficiency and consistency.
Budget: Cost Considerations
If budget constraints are a primary concern, sand casting is generally a more economical choice compared to other casting methods. The lower cost of molds and the ability to use less expensive materials can have a significant impact on overall production costs.
Production Timeline: Speed of Manufacturing
Sand casting may not be the fastest method due to the time required to create molds and the cooling period for the metal. If your production timeline is tight, you may need to explore faster alternatives or ensure that sand casting can meet your delivery schedule.
Shape: Complexity and Design
One of the strengths of sand casting is its ability to produce complex shapes and large parts. If your product has intricate designs or requires a large size, sand casting can be an effective manufacturing solution.

The Benefits of Choosing Sand Casting for Metal Fabrication
Sand casting is a well-established and widely utilized method in the metal fabrication industry. This process offers several distinct advantages that make it particularly appealing for certain types of manufacturing projects. Here’s a deeper dive into the benefits of using sand casting:
Cost Efficiency for Low-Volume Production
One of the most significant advantages of sand casting is its cost-effectiveness, especially when it comes to low-volume production runs. The cost of creating molds for sand casting is relatively low, and the process does not require expensive equipment or materials. This affordability makes sand casting a practical choice for small batch manufacturing, where the economies of scale associated with high-volume production do not apply.
Fabrication of Large Parts
Sand casting is exceptionally suitable for producing large parts and components, which might be challenging or cost-prohibitive to fabricate using other casting methods. The flexibility of the sand mold allows for the creation of sizable castings without the constraints often faced with alternative processes.

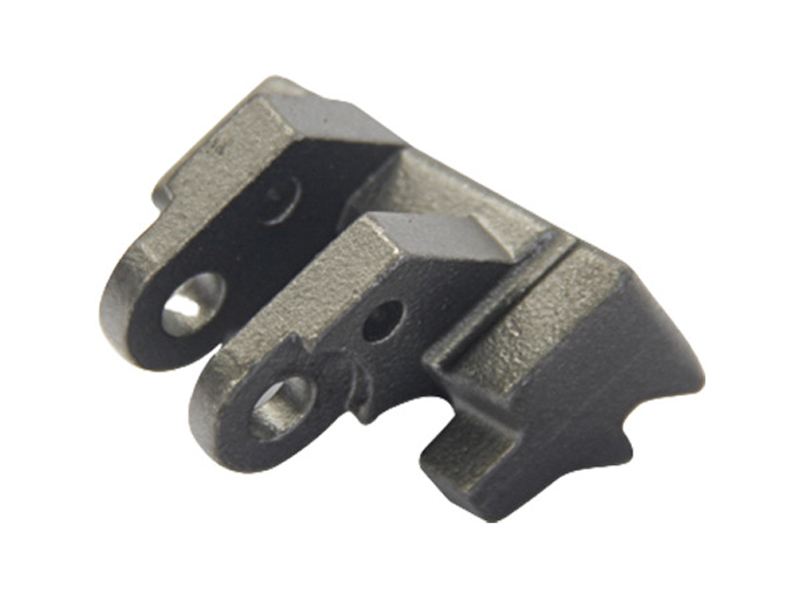
Dimensional Accuracy and Tolerances
While sand casting can achieve good dimensional accuracy, it may not be as precise as other casting methods. If your product requires tight tolerances, consider if the capabilities of sand casting can meet the specifications or if another process would be better suited.
Surface Finish: Aesthetics and Functionality
Sand casting typically results in a rougher surface finish compared to other methods. If your product demands a smooth surface or if the finish is critical for functionality, additional post-processing may be needed, or you might need to choose a different manufacturing process.
Image Above: A Clevis Manufactured Via Sand Casting
The image depicts a clevis produced through sand casting, showcasing the process's ability to create robust, functional parts. However, as with any part or product, it's crucial to weigh the benefits and limitations of sand casting before committing to this method.
In conclusion, sand casting offers a range of advantages for certain types of products, especially those that require versatility in shape and are produced in smaller quantities. By carefully considering factors like quantity, budget, production timeline, shape, dimensional accuracy, tolerances, and surface finish, you can determine if sand casting is the appropriate manufacturing process for your product. If you're uncertain, consulting with a sand casting expert or manufacturer can provide clarity and guide you to the most suitable production strategy for your needs.
Versatility with Metal Types
Another advantage is the ability to work with a broad spectrum of metals, whether ferrous or non-ferrous. Sand casting accommodates materials including, but not limited to, iron, steel, aluminum, bronze, and brass. This versatility ensures that manufacturers can select the most appropriate metal to meet the specific requirements and performance characteristics of the final product.
Shorter Lead Times
When compared to other casting techniques, sand casting often has shorter lead times. The relatively straightforward process of creating sand molds and the minimal need for specialized tooling contribute to faster turnaround times from design to production. This can be crucial for projects with tight deadlines or for companies looking to bring their products to market swiftly.
Low Initial Setup Cost
The initial setup cost for sand casting is among the lowest of all casting processes, making it a highly attractive option for new projects or for companies exploring the feasibility of a new part without a significant upfront investment. The affordability of setup also makes sand casting an excellent choice for prototype development, where the design may undergo several iterations before finalization.
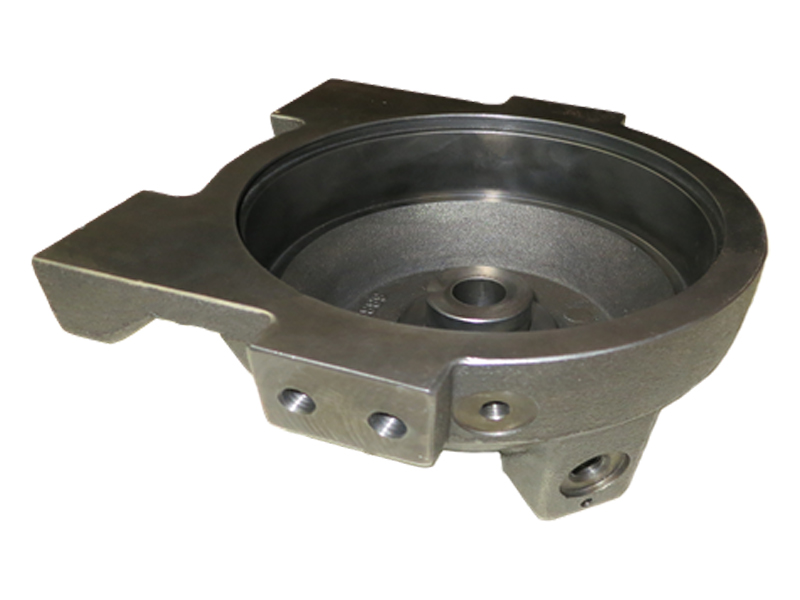

Ease of Modification
Modifications to the sand casting process are relatively easy to implement. Adjustments to the sand mold can be made without incurring significant costs, which is particularly beneficial when design changes are required. This flexibility in mold alterations allows for ongoing design improvements and can significantly reduce the cost associated with design changes.
Ideal for Low- to Medium-Volume Production and Prototypes
Due to its low setup costs and adaptability, sand casting is ideal for fabricating parts in low- to medium-volume runs. It is also well-suited for creating prototypes that may later transition to higher-volume production methods. Additionally, sand casting can be employed to convert welded parts into castings, which can result in cost savings and improved structural integrity.
In summary, sand casting offers a combination of cost savings, flexibility, and versatility that is unmatched by many other metal fabrication processes. Its ability to produce large parts, work with various metals, and accommodate design changes, all while maintaining lower costs and shorter lead times, makes sand casting a preferred method for manufacturers across a range of industries. Whether for prototyping, low-volume production, or the conversion of welded components, the advantages of sand casting are clear and compelling.