Plastic Extrusion Services
The Fundamentals of Plastic Extrusion: A Comprehensive Overview
Plastic extrusion is a manufacturing technique that transforms raw thermoplastic granules into a continuous profile with a uniform cross-section. This process is key to creating a diverse range of plastic products used across various industries. Here's a closer look at how plastic extrusion works and its significance in the manufacturing landscape.
The Plastic Extrusion Process Explained
Imagine plastic extrusion as a sophisticated version of pushing playdough through a mold to create different shapes—except, in this case, the playdough is thermoplastic granules, and the mold is a high-precision die.
The process begins with the feeding of these granules into a hopper, which then directs them into the barrel of an extruder. Within the barrel, a heated rotary screw—akin to the one found in plastic injection molding machines—applies both heat and pressure. As the granules are conveyed by the screw, they rub against each other and the inner walls of the barrel, causing the plastic to heat up and eventually melt into a viscous, molten state.


Once the thermoplastic is sufficiently molten, it's pushed through a fine filter to remove any contaminants, ensuring a clean and pure extrusion. The molten plastic then enters the die, which is specifically shaped to form the desired cross-sectional profile. As the plastic exits the die, it retains the shape of the die's opening, becoming the final extruded product.
This newly formed extrusion is continuously drawn away from the die at a constant rate, allowing it to cool and solidify. Cooling is typically achieved by passing the extrusion through a water bath or by using air-cooling methods. Finally, the extruded plastic is cut into standard lengths for sale and distribution, ready to be transformed into the final products.
Plastic Tubing and Enclosed Profiles
Plastic extrusion is particularly adept at creating tubing, which features an enclosed profile that can be likened to an open cavity, known as a lumen. Tubing is versatile and can be designed with multiple lumens, dividing the internal space into separate channels while maintaining consistent wall thickness throughout. At LK tools, for example, plastic extrusions can be crafted with up to 4 lumens, catering to more complex application requirements.
Applications Across Industries
The utility of plastic extrusions extends across nearly every sector, from construction materials like PVC piping to telecommunications conduits, from automotive components to medical device tubing. The inherent benefits of plastic—such as lightweight, flexibility, durability, and resistance to corrosion—make extrusions indispensable in countless applications.
Illustration of Plastic Extrusion Process
An illustration of the plastic extrusion process can be helpful to visualize the melting and extrusion stages. It showcases the transformation from solid granules to molten plastic and finally to the extruded product, emphasizing the seamless nature of this manufacturing method.
In summary, plastic extrusion is a critical process in today's manufacturing world, enabling the mass production of consistent, high-quality plastic profiles. Its versatility and efficiency make it a foundational technique for creating components that are integral to a wide array of products and services in our daily lives.


Maximizing Efficiency with LK tools's Plastic Extrusion Services
Plastic extrusion is a highly efficient method for producing custom profiles, and when it comes to streamlining your manufacturing process with precision and customizability, LK tools stands out as a prime partner. Here’s how LK tools's plastic extrusion services benefit designers and manufacturers.
Customization and Variety
LK tools allows for an impressive level of customization, enabling designers to specify the exact profile and colors required for their plastic extrusion needs. Whether you're creating complex channels for wiring or simple PVC pipes, LK tools's services ensure that the final product matches your intended use perfectly.
Ease of Design Integration
With LK tools’s Instant Quoting Engine, integrating your design into the manufacturing process is a breeze. You can simply upload your CAD files in various formats, including STEP, STP, JT, SLDPRT, IPT, PRT, and SAT, among others. Instantly, you'll receive a quote that provides estimated costs, lead times, and options for materials, finishes, and packaging. This seamless integration eliminates guesswork and allows for efficient planning and budgeting.
Rapid Production and Delivery
LK tools’s Manufacturing Supplier Network is designed to expedite your manufacturing process, significantly boosting turnaround times. You can choose from standard, expedited, or economy shipping options to align with your project schedule. Moreover, with both domestic and international manufacturing capabilities within LK tools's network, you'll find a solution that fits your location and timeline. LK tools can transition from die creation to part production in just a few weeks.
Cost-Effective Production
One of the major advantages of plastic extrusion is the potential for cost savings. Thoughtfully designed extrusions can often replace multi-part assemblies, thus reducing the total cost of your project. High-volume production runs are not only feasible but also cost-effective, making plastic extrusion a smart choice for large orders.
Furthermore, the relative simplicity of the extrusion process translates into significantly lower tooling costs—often 80-90% less—compared to other manufacturing methods like injection molding or die casting. This cost efficiency makes plastic extrusion an appealing option for projects where high volume and low cost are essential.
In essence, LK tools's plastic extrusion services combine the benefits of customization, ease of design integration, fast production, and cost-effectiveness. By choosing LK tools for your plastic extrusion needs, you can expect a smooth, streamlined process from design to delivery, ensuring that your project stays on track both in terms of time and budget. Whether you're in the initial stages of design or ready to start production, LK tools's platform is equipped to support your plastic extrusion project every step of the way.


Custom Plastic Extrusion Shapes and Their Multitude of Applications
Plastic extrusion is a versatile manufacturing process capable of producing a wide range of shapes and profiles that are integral to countless applications. With the ability to conform to various open and closed configurations, plastic extrusion is a valuable tool for designers and manufacturers in nearly every industry.
Plastic Extrusion Shapes
The potential shapes achievable through plastic extrusion are diverse. The most commonly utilized profiles are simple annular or square tubes and pipes that adhere to industry standards, ensuring compatibility with fittings and other system components. LK tools's plastic extrusion services excel in producing enclosed profiles, offering up to 4 lumens within a single extrusion. This capability allows for the subdivision of internal space to accommodate multiple channels within the same profile, enabling complex designs and functions.
Beyond the closed shapes, plastic extrusions can also be fabricated into open profiles such as U, J, or L channels. These shapes are tailored to specific design requirements and are useful in a variety of structural and aesthetic applications.
Plastic Extrusion Applications
The applications for plastic extrusions span across numerous sectors. Here are some of the typical uses:
Electrical Conduits: Plastic extrusion is ideal for creating conduits that house and protect electrical wiring, offering additional insulation and safeguarding against damage. These conduits are commonplace in residential, commercial, and industrial settings, and plastic variants provide an advantage by preventing short circuits that might occur with metal conduits.
Non-corroding Pipes: Perhaps one of the most prevalent uses of plastic extrusion in industry is the fabrication of pipes for transporting water, waste, and other fluids. Plastic pipes are impervious to corrosion caused by chemicals or water exposure, giving them an edge over traditional materials like copper, cast iron, and steel in plumbing and irrigation systems.
Weatherstripping and Trim: Plastic extrusions are frequently employed to create weatherstripping and trim for various applications. These extruded parts can seal out weather elements, cover sharp edges, and enhance the durability and appearance of products. This use is widespread across consumer goods, the automotive industry, and industrial equipment.
Designers and manufacturers turn to plastic extrusions for their ability to meet specific design criteria and functional needs. The adaptability of plastic extrusion makes it a preferred method for creating custom parts that must withstand environmental factors, carry fluids without degradation, or provide precise finishing touches to products.
By harnessing the capabilities of plastic extrusion, industries can benefit from the lightweight, durability, and cost-effectiveness of custom plastic parts. Whether for standard applications or innovative new uses, plastic extrusion continues to play a crucial role in the development and production of components that meet the evolving needs of today's markets.
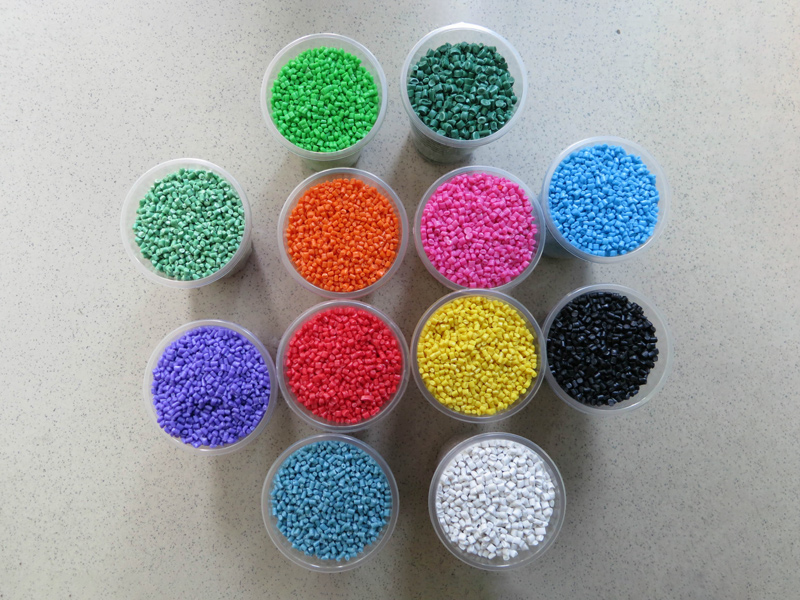

Weighing the Pros and Cons of Plastic Extrusion
Plastic extrusion is a transformative manufacturing technique used to create a plethora of components across industries. Understanding the advantages and potential drawbacks of this process is essential for manufacturers when deciding if it is the right method for their project. Here’s an assessment of the pros and cons associated with plastic extrusion.
Advantages of Plastic Extrusion
Dimensional Accuracy and Stability: Modern extrusion technology allows for the production of extruded shapes with close tolerances, resulting in durable and dimensionally stable parts. The process caters to a range of materials, from rigid and pliable plastics to elastomers.
Low Part Cost: Thoughtful design can lead to extruded parts that replace complex assemblies, reducing the number of components and overall cost. High production volumes are not only attainable but also cost-effective.
Lower Tooling Cost: Compared to other manufacturing processes such as injection molding, plastic extrusion offers significantly lower tooling costs, typically 80-90% less, which is particularly beneficial for high-volume production.
Part Complexity: Extrusion excels at creating parts with intricate cross-sectional shapes. This includes complex features like undercuts, T-slots, interior channels, and grooves that are often required in sophisticated designs.

Disadvantages of Plastic Extrusion
Initial Setup Cost: While the cost per part is low, the initial setup entails expenses related to tooling, establishing the production line, and meeting material minimums.
Design Limitations: Despite its ability to produce complex profiles, extrusion has certain design constraints. The constant cross-section of the extrusion means that features such as countersunk holes and pockets are not possible without secondary machining operations.
Lead Times: The number of manufacturers specializing in extrusion is limited, as the process requires substantial machinery and facility investments. Additionally, creating and iterating dies can be a lengthy process. Consequently, the lead time for initial part delivery is typically between four to six weeks.
In summary, plastic extrusion presents a range of benefits, including cost savings, part complexity, and dimensional stability, making it a viable option for a variety of applications. However, it's important to consider the initial setup costs, design constraints, and lead times that come with this manufacturing method. By carefully evaluating these factors, manufacturers can make informed decisions about the suitability of plastic extrusion for their projects. For a more in-depth understanding of plastic extrusion design considerations, refer to specialized blog posts and resources that provide expert insights into optimizing your designs for this process.