Design
Embracing Versatility with Live Tool Lathes and Design Aids at LK tools
At LK tools, our manufacturing capabilities extend beyond precise milling; we also provide live-tool CNC turning to cater to a variety of design needs. The toolsets on our live-tool lathes are similar to those used in our machining centers, enabling us to create off-center holes, slots, flats, and other features that are machined parallel or perpendicular to the turned workpiece's Z-axis. These follow the same design rules as parts produced on our machining centers, with the primary difference being the shape of the raw material. Turned parts like shafts and pistons typically start from round stock, while milled parts such as manifolds, instrument cases, and valve covers usually originate from square or rectangular blocks.
Design Aids for Enhanced Learning:
Understanding the nuances of manufacturing processes can be greatly improved with tangible examples and educational tools. To help with this, LK tools offers free design aids that delve into the design elements, materials, and surface finishes of injection-molded parts.


Material Selectors: Your Pocket-Sized Guide to Choosing the Right Materials
For designers and engineers planning their next project, selecting the appropriate material is crucial for success. To assist in this critical step, our pocket-sized Material Selectors serve as quick reference guides, making it easy to determine the ideal plastic or metal for your specific needs.
These handy Material Selectors provide detailed information on various properties, such as strength, flexibility, heat resistance, and more, allowing you to compare and contrast the characteristics of different materials at a glance. By consulting these guides, you can ensure that the material you choose aligns perfectly with the requirements and application of your part.
Whether you're in the workshop, at your desk, or on the go, these Material Selectors are an essential tool for anyone in the manufacturing industry looking to make informed decisions about material and process selection for their projects.
Design Cube:
One of the most effective ways to comprehend the injection molding process is by examining a physical part. The Design Cube is an innovative tool that illustrates common design mistakes, such as features that are too thin or too thick, poorly designed bosses, and the dos and don'ts of rib construction. It's an invaluable resource for designers to physically assess the impact of their design choices.
Demo Mold:
For those new to the world of injection molding, the Demo Mold is an insightful design aid that demonstrates the interaction between the A-side and B-side of a mold during the plastic part creation process. This tool is not only educational for beginners but also serves as an excellent teaching aid for instructors in the field.
By leveraging these design aids, engineers and designers can gain a clearer understanding of the intricacies of injection molding and how to optimize their designs for this process. LK tools is dedicated to providing the resources and expertise needed to transform your innovative ideas into tangible, high-quality parts.


Essential Design Tips for Optimal CNC Machining
When embarking on the design process for CNC machining, it's imperative to adhere to certain principles that ensure precision and accuracy, resulting in high-quality parts. There are established general design rules recommended for the most common features found in CNC machined parts. It's these guidelines that can make a significant difference in the manufacturability and functionality of the final product.
These rules cover a wide range of design aspects, including but not limited to, the selection of tolerances, the minimization of complex geometries, the reduction of the number of tool changes required, and the consideration of the limitations of the CNC machine itself. By following these best practices, designers can avoid common pitfalls that may lead to production issues or compromised part quality.
Understanding and applying these CNC machining design rules early in the design process can save time, reduce costs, and ensure that the end result meets or exceeds performance expectations. Whether you're a seasoned engineer or a novice designer, these tips are crucial for creating designs that are not only feasible but also optimized for CNC machining.
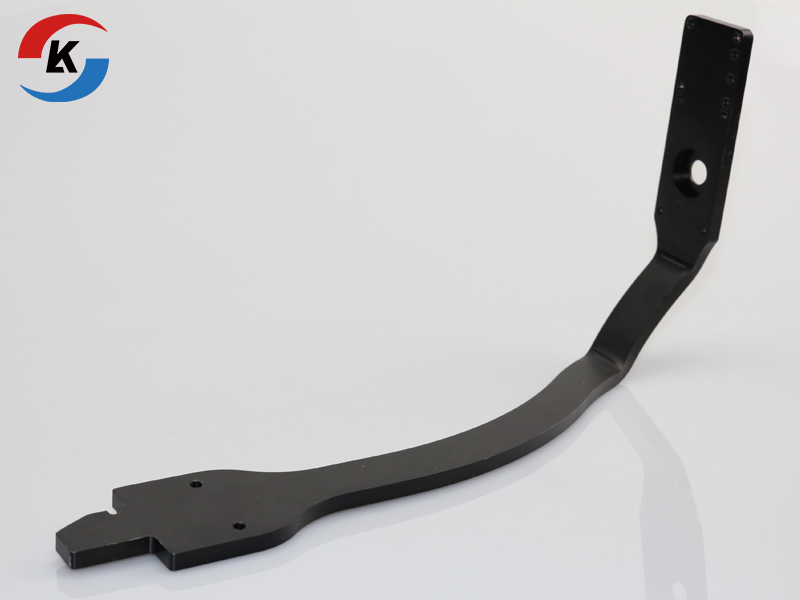
CNC Machining Best Practices: Maintaining Adequate Wall Thickness
In the realm of CNC machining, it's critical to avoid creating excessively thin walls in your designs. Thin walls can significantly compromise the stiffness of the material, leading to a reduction in the precision of the machined part due to vibrations that occur during the machining process. To maintain structural integrity and accuracy, there are standard minimum wall thicknesses that designers should adhere to.
For metal parts, the recommended minimum wall thickness is 0.794 mm, while for plastic components, the minimum is set at 1.5 mm. These guidelines help ensure that the parts can withstand the stresses of machining without deformation or loss of detail.
If your design necessitates walls thinner than these standards, it may be beneficial to consider alternative manufacturing processes that are more suited to such requirements. Sheet metal fabrication, for example, can be a more suitable and cost-effective method for producing parts with very thin walls. By selecting the appropriate manufacturing process for your design, you can achieve the desired results without compromising on quality or incurring unnecessary costs.
Designing for CNC Machinability: Steering Clear of Unmachinable Features
When creating designs for CNC machining, it's essential to recognize the limitations of the tools at your disposal. Certain features are simply not achievable with conventional CNC mills, lathes, or drills. A prime example of such a feature is "curved holes," which are beyond the capabilities of standard CNC equipment.
If your design requires curved holes or other complex features that traditional CNC machining can't produce, it's worth considering alternative manufacturing techniques. Electrical discharge machining (EDM) is an excellent option for creating intricate shapes and detailed features that are otherwise impossible to machine. EDM uses electrical sparks to erode material in a very controlled manner, allowing for the production of complex geometries with precision.
By understanding the constraints of CNC machining and being open to alternative methods like EDM, you can ensure that your designs remain feasible and can be brought to life without compromising on the intricate details that may be critical to the part's functionality.


Smart Tolerance Selection in CNC Machining for Efficiency and Cost-Effectiveness
When drafting designs for CNC machining, it's important to be judicious with the application of tight tolerances. Defaulting to the standard tolerances of the CNC machine can often save significant time and expense in the production process. These standard tolerances are the norm for a reason—they balance precision with practicality.
Tight tolerances should only be specified when the success of the part's function hinges on high accuracy. Overuse of tight tolerances can lead to unnecessary complexity and increased costs, both in terms of machining time and the potential need for more advanced equipment or additional processes.
If your design does require tight tolerances for certain features, it's crucial to apply them consistently across the design. This consistency helps streamline the machining process, as the equipment can be set up to meet these precise requirements without the need for frequent adjustments. By thoughtfully applying tolerances only where they are critical, you can optimize your design for both manufacturability and cost-efficiency.
Streamlining CNC Machining by Focusing on Essential Features
When designing parts for CNC machining, it's crucial to differentiate between necessary functional features and those that are purely aesthetic. While aesthetics are important, some visually appealing features may not be practical or cost-effective to machine. As a designer, it's beneficial to consider the manufacturing implications of each feature by asking questions such as, "What CNC machining process would be needed to create this feature?" or "Does this require the capabilities of a 5-axis or a 3-axis machine?"
Enhance your design by prioritizing the precision of essential features over aesthetic embellishments. Remember that the primary goal of CNC machining is to achieve accuracy and functionality. If aesthetic modifications are desired, it's often more efficient to apply them as post-machining processes, such as anodizing, painting, or polishing. By focusing on the fundamental aspects of your design and employing post-machining techniques for aesthetic purposes, you can streamline the manufacturing process and potentially reduce costs.


Mastering Design for Manufacturing: The Essentials of Drilling and Beyond
The 'Hole' Truth About Drilling at LK tools:
Frequent visitors to any workshop are no strangers to the humble drill bit and its purpose. However, at LK tools, we've taken a different approach to creating holes by using an endmill for interpolation rather than traditional drilling. This method significantly enhances flexibility, allowing for a variety of hole sizes with just one tool and yielding a smoother surface finish than is typically achievable with drilling. An added bonus is that the same endmill can be employed for machining slots and pockets, which streamlines the production process by reducing cycle times and cutting down on part costs. The only limitation to consider is that drilling holes more than six times the diameter of the endmill poses a challenge due to the tool's length restrictions, potentially necessitating machining from both sides of the part.
Navigating Manufacturing Design: Tips for Cost Savings and Flawless Production
Cost Reduction:
Small changes in your design can lead to big savings. By tweaking certain aspects of your design, you can reduce both the time and money spent on production without compromising on quality.
Defect Prevention:
Design defects are an unfortunate reality, but with the right knowledge, you can avoid the most troublesome ones. Being proactive in your design approach is crucial to minimize the risk of costly mistakes.
Basic Design Principles:
When in doubt, stick to the basics. Occasionally, a quick review of the fundamental elements of your design can provide the clarity needed to move forward confidently.
Complex Design Challenges:
Once you've mastered the basics, it's time to tackle the more complex aspects of design modeling. Understanding how to handle intricate geometries and features is essential for advanced manufacturing projects.


Design Tips for Efficient Manufacturing:
When it comes to creating plastic, metal, and elastomeric components for processes like injection molding, CNC machining, 3D printing, and sheet metal fabrication, keeping manufacturability at the forefront of your design is crucial. By considering how your part will be made during the design phase, you can significantly speed up production and decrease costs. This proactive mindset involves selecting appropriate materials, simplifying geometries, and anticipating potential manufacturing challenges to ensure a smooth transition from design to finished product. Whether you're drilling a simple hole or crafting a complex multi-faceted part, these design tips are the keys to unlocking efficiency and cost-effectiveness in manufacturing.
Designing with Plastics:
With a diverse range of over 130 plastics used in our services, each material presents unique benefits and potential complications. Our design tips will help you navigate these nuances and prepare for any challenges.
Metal Part Design:
Designing with metal requires careful consideration of factors like sharp edges and corrosion. Our tips provide guidance on how to design metal parts that are both safe and durable.
Threading Right:
In manufacturing, drilling and threading are often intertwined. While traditional shops use taps to create internal threads, our modern approach involves a thread mill. This tool allows for accurate threading and the ability to cut any thread size with the same pitch using a single tool. This not only saves on production time but also simplifies setup processes. We can produce a wide range of UNC and UNF threads, from #2 to 1/2 inch, as well as metric threads from M2 to M12, using just one set of tools.
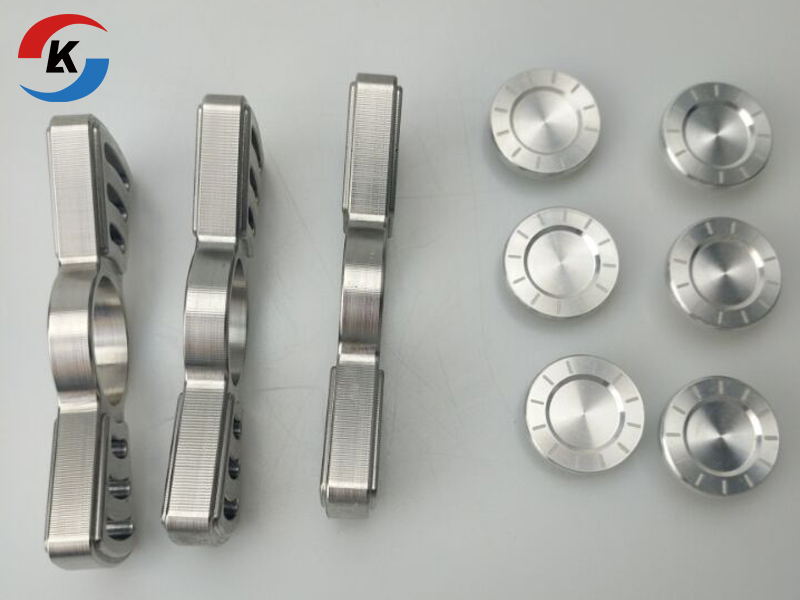

Enhance Your Manufacturing with Expert Design Essentials
To support your manufacturing endeavors, we've curated a collection of crucial design insights into three comprehensive guides, each tailored to a specific production process: 3D printing, machining, and molding. These guides are packed with actionable tips aimed at enhancing manufacturability, reducing production costs through intelligent design and material selection, and addressing various other aspects of the manufacturing workflow.
Adding Text to Your Parts:
If you're looking to incorporate a part number, description, or logo onto your machined parts, LK tools has the capability to mill virtually any text you require. For optimal results, ensure that the spacing between characters and the thickness of the lines used to create the text is at least 0.020 inches
Navigating the Challenges of Machining Tall Walls and Tiny Features
In the world of manufacturing, crafting parts with tall walls and tiny features requires precision and a deep understanding of both the materials and the tools used. At LK tools, our arsenal includes carbide cutting tools known for their exceptional rigidity, which ensures maximum tool life and productivity while minimizing deflection during the machining process.
Despite the strength of these tools, deflection is an inevitable occurrence, affecting not only the tools but also the metals and plastics being machined. This means that the success of machining tall walls and small features largely depends on the specific geometry of the part and the capabilities of the toolset in use. For example, although the minimum feature thickness we can achieve is 0.020 inches (0.5mm) and the maximum feature depth is 2 inches (51mm), designers must consider the limitations these dimensions may impose on more complex structures, such as a ribbed heatsink.

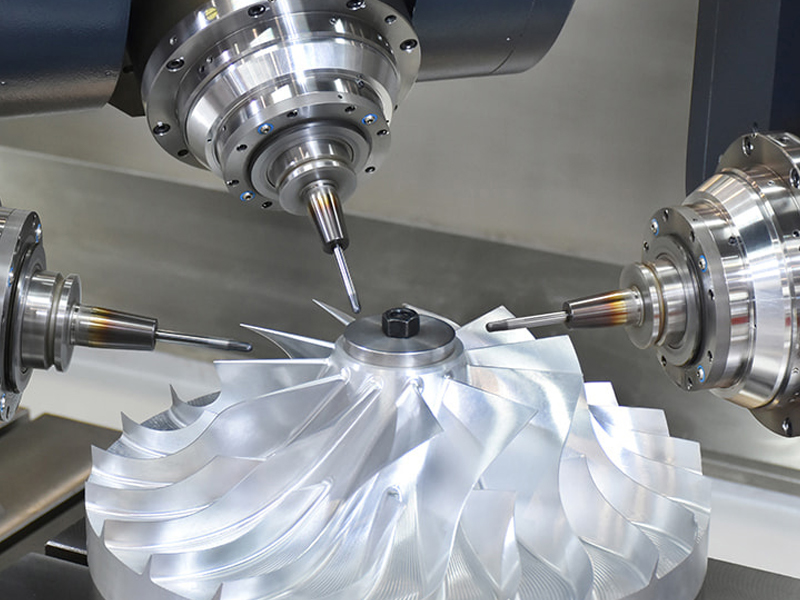
(0.5mm). To guarantee legibility and durability, we recommend that the text be recessed into the part rather than raised. Additionally, for the clearest and most readable text, we suggest using fonts that are 20-point or larger, specifically clean and simple Sans-Serif fonts such as Arial or Verdana.
These specialized tips, along with the wealth of knowledge contained within our design guides, are readily available for download. They serve as an invaluable resource for designers and engineers looking to optimize their parts for the realities of modern manufacturing. Whether you're a seasoned professional or just starting out, our design essentials offer the guidance necessary to refine your projects for success.
Featured Design Tips:
Why You Should Use Vapor Smoothing on 3D-Printed Parts:
Vapor smoothing is a finishing technique that employs chemical vapors to enhance the surface quality of 3D-printed parts, eliminating imperfections and creating a smoother appearance.
Solving Wall Thickness Issues in Molded Parts:
When faced with design change requests, particularly concerning slot widths and wall thicknesses in molded parts, it's essential to address these issues head-on to ensure manufacturability and function.
Finding the Right Corrosion-resistant Metals:
Combat the effects of corrosion by selecting materials that can withstand harsh environments and prevent your parts from deteriorating into rust.
By reading our design tips, you can gain valuable insights into how to optimize your designs for the realities of the manufacturing process, whether you're dealing with 3D printing, molding, or machining.
